Deep Freezer Cooling problem
- SJ DynaMark
- Jun 10, 2024
- 2 min read
Updated: Jun 24, 2024
Deep freezer units are crucial for preserving perishable goods, but what happens when they fail to maintain the required temperatures? In this blog post, we explore a common cooling issue faced by rebuilt companies and how it was successfully resolved.
At our rebuilt company, ensuring the reliability of deep freezer units is paramount. These units are designed to operate at extremely low temperatures to keep products frozen and safe for extended periods. However, like any complex system, they can encounter issues that affect their performance.
One of the most significant problems we faced was a cooling issue in our deep freezer units. Customers reported that their units were not maintaining the necessary temperatures, leading to potential spoilage of valuable inventory. This problem not only threatened the quality of stored goods but also risked the reputation of our rebuilt company.
The root cause of this issue was traced back to several factors, including:
Inadequate insulation
Faulty cooling components
Improper maintenance practices
These factors combined to create a situation where the deep freezer units were unable to sustain the required cold temperatures, leading to frequent complaints and service calls.
Addressing this cooling issue required a comprehensive approach.
Here’s how we tackled the deep freezer cooling problem:
Improved Insulation:
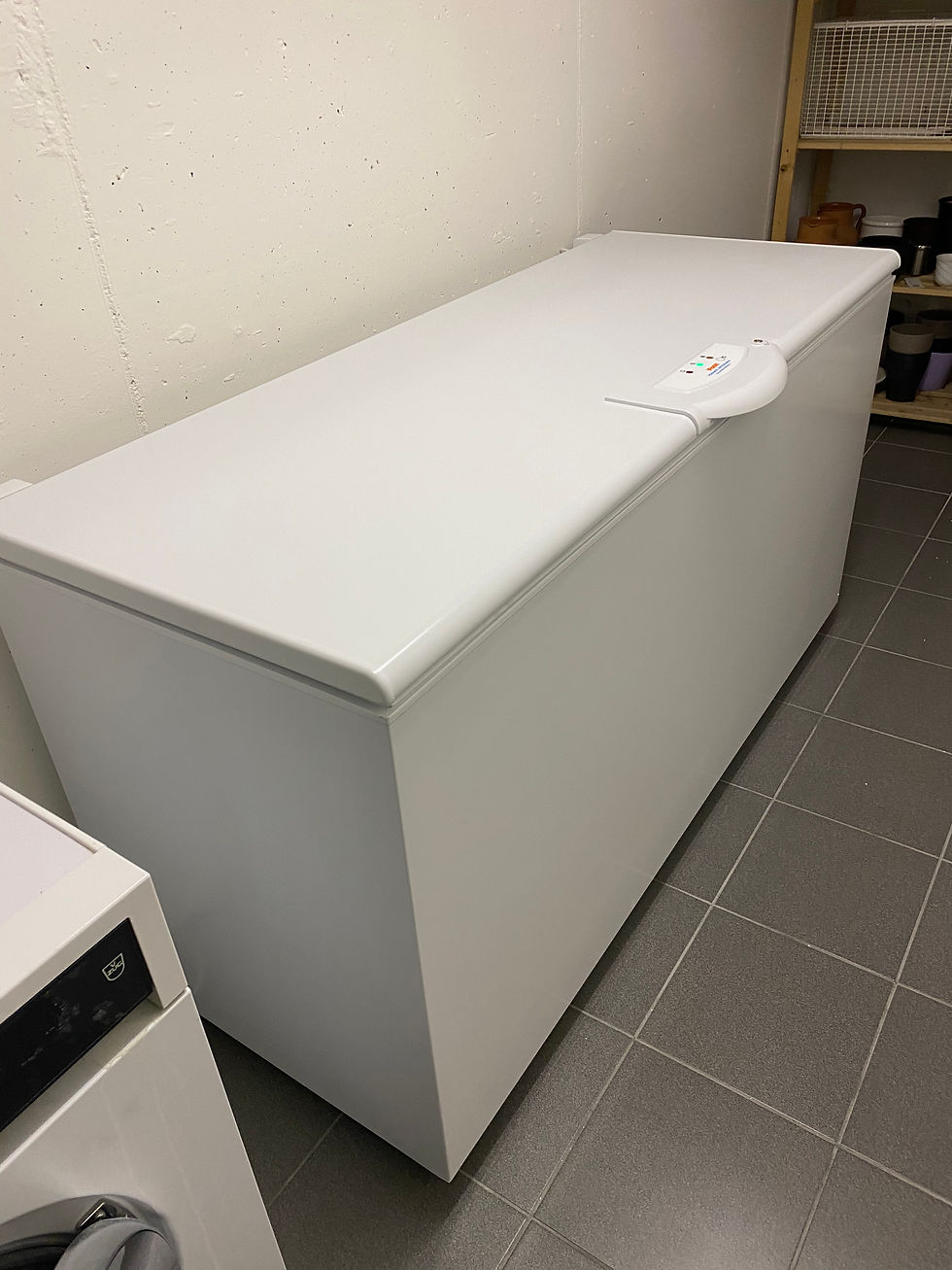
We upgraded the insulation materials used in the deep freezer units to enhance their ability to retain cold air. This step significantly reduced temperature fluctuations.
Component Overhaul:
Faulty cooling components were identified and replaced with high-quality, durable parts. This ensured that the cooling systems operated efficiently and consistently.
Regular Maintenance:
We implemented a rigorous maintenance schedule to proactively address potential issues before they escalated. Regular inspections and servicing helped maintain optimal performance.
Customer Education:
Educating our customers on proper usage and maintenance of deep freezer units was also crucial. We provided guidelines and tips to help them avoid common pitfalls that could lead to cooling problems.
By taking these steps, we not only resolved the immediate cooling issues but also enhanced the overall reliability of our deep freezer units. Our customers could now trust that their products would remain safely frozen, thereby protecting their investments and our company's reputation.
The journey to resolve the deep freezer cooling problem was challenging but ultimately rewarding. Through targeted improvements and proactive measures, our rebuilt company was able to overcome this obstacle and deliver reliable, high-performing deep freeze units to our customers. This experience reinforced the importance of quality, maintenance, and customer education in ensuring the success of our products.
Comentarios